solid tungsten carbide end mill
solid carbide end mill CNC router bits for steel, aluminum, stainless steel(SUS), graphite, copper etc..
Engineered Carbide End Mill Solution
With decades of experience in designing and manufacturing carbide end mill cutter bits, Sundi provides expert support to machining manufacturers. Our engineering expertise and intelligence enable us to create custom-engineered solutions for any quantity, big or small, to improve productivity.
Our Mission
Our goal is to achieve total customer satisfaction through the endless pursuit of excellence in solutions, quality, and service.
Our Capacity
We offer a wide range of carbide end mill cutter bits for roughing and finishing operations, available in standard or special designs. They can be manufactured as solid carbide or with coolant capabilities.

We Are One Of Best Carbide End Mill Maker
Sundi designs and manufactures tungsten carbide end mills for clients around the world in various industries. Our end mills are suitable for rough or precision processing of materials such as copper, copper alloys, cast iron, carbon steel, mild steel, stainless steel, titanium alloys, nickel alloys, aluminum, aluminum alloys, plastics, heat-treating steel, and more, to achieve the required finish and accuracy of parts.
Whether for milling, turning, or drilling processes, our proven full product life cycle process enables us to optimize tools. We specialize in developing cutting tool solutions to improve the quality of products and increase production efficiency for our clients. They can be manufactured as solid carbide or coolant.
- High Accuracy and Efficiency
- High-speed Cutting Feed Rate
- Excellent Roughness
- Fewer Process Steps Low cycle time
- Maximum tool life
- Re-grinding to reduce the cost
find the carbide end mill set with different form
Connect Us Now
find the carbide end mill bits with different application
Material Application of Carbide End Mill Cutter
Connect with the Sundi Tools Sales Team
Application of Carbide end mill Cutter
Carbide end mill cutters are versatile tools used in CNC machines, engraving machines, and standard milling machines to process heat-treated hard and moderately complex materials. Their hardness usually ranges from HRA93-97, almost as hard as diamonds, which makes them durable and brittle for specific applications. They are also not annealed, making them suitable for a wide range of jobs.
Aerospace
Automotive
Medical
Machinery
What made us different
-
7×24 Hrs
7x24Hrs online for technical support
-
Design
Re-design and 3D mold building
-
cost reduce
The same quality compared with the top-brand, but half or quarter cost.
-
3 Days
Fast reaction as fast as 3 days from drawing approval to delivery
-
Express shipping
Worldwide shipment (UPS,DHL,FedEx,TNT)
-
1 year Warranty
Quality assurance and after-sales without worries for as long as 12months
High-Level Qualified Raw Material
We source our tungsten carbide rods from Japan or Germany to ensure top quality. Our end mill set, with its consistent material performance, surpasses comparable products on the market.
Un-equal flutes Design against the Vibration
End mill sets with flutes that have sharp cutting edges and an unequal design can increase cutting efficiency by up to 300% due to their anti-vibration design.
OEM Service
Through our OEM service, we help you brand your own logo or packaging.

Advanced Production Techniques
The use of chamfered radius helps to prevent tool collisions while Walter machines ensure consistent dimensions in our production process.
World-class Coating Service-BALZERS
We are dedicated to offering our customers world-class coating services and constantly introduce new technologies to extend the service life of our products.
Custom-Made Service
Our competent technical team offers unique machining solutions through our custom-made service.
Common the end mill Coating Performance
COATING | Color | Hardness | MAX.working Temp | coated thickness |
---|---|---|---|---|
TIN | Bronze | 2400HV | 600°C | 1-7μm |
TIALN | Violet Black | 3500HV | 800°C | 1-4μm |
TISIN | Bronze | 3900HV | 1000°C | 2-4μm |
DLC | Black | 2800HV | 400°C | 1-3μm |
NACO BLUE | Blue | 4500HV | 1200°C | 2-3μm |
DIAMOND | Black | 10000HV | 800°C | 0.5-1.5μm |
TICN | Black Grey | 3200HV | 400°C | 1-4μm |
User Case of Carbide End Mill Cutters
Diamond coating milling cutter for graphite
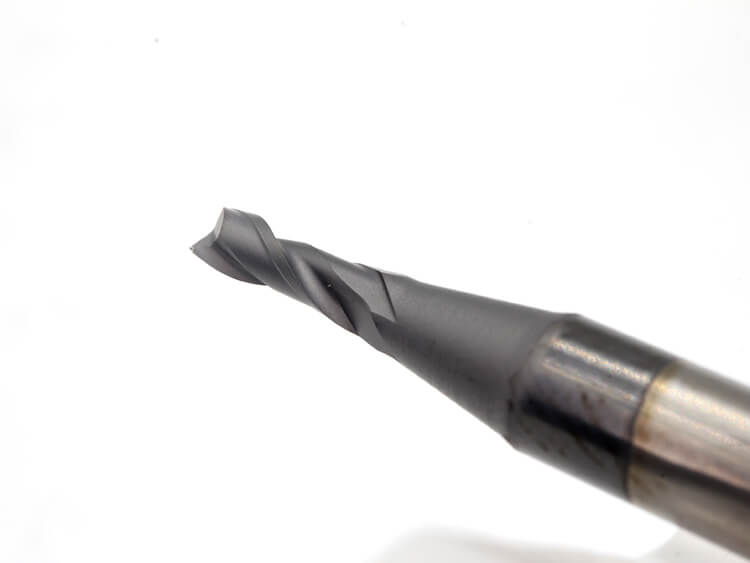
5.7 x
1.3 x
-
D780
Used Tool
-
Graphite
working material
-
Finish Machining
Process
-
110m/min
Cutting speed
-
800mm/min
Feed
-
emulsion
Coolant
Ball nose milling cutter for aluminum
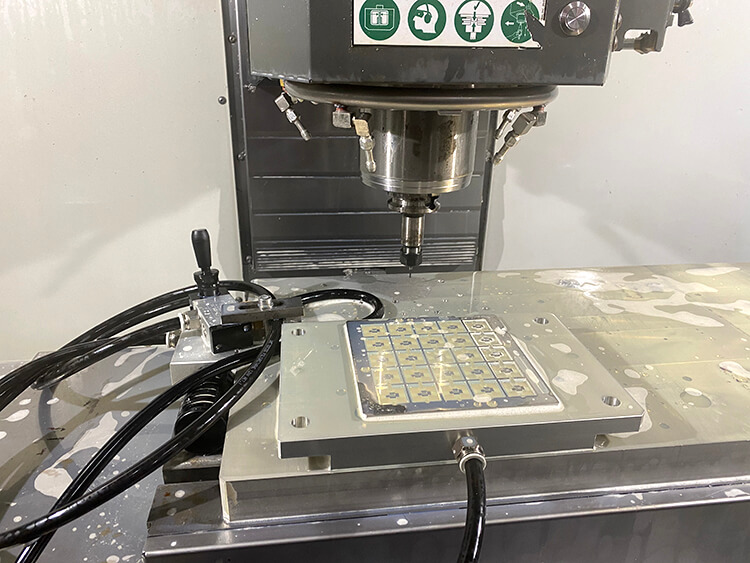
10.3 x
5.4 x
-
AL550
Used Tool
-
aluminum
working material
-
Profile machining
Process
-
150m/min(8000 min)
Cutting speed
-
1500mm/min
Feed
-
emulsion
Clooant
Ball nose milling cutter for hard steel
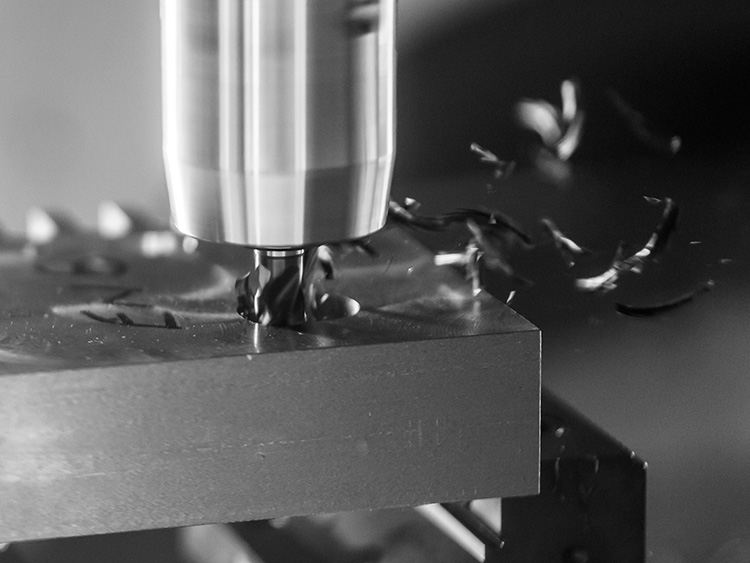
2.0 x
1.2 x
-
S650
Used Tool
-
Steel HRC60
working material
-
Profile machining
Process
-
150m/min(8000 min)
Cutting speed
-
1500mm/min
Feed
-
emulsion
Clooant
Connect Us Now
the steps show How we made the carbide end mill
-
Step 1: Analysis And Design
-
Step 1: Analysis And Design
By thoroughly communicating with our customers and gaining a deeper understanding of their requirements, including accuracy, roughness, and tool lifespan, we can fabricate high-quality carbide milling tools tailored to specific applications.
-
Step 2: Suitable Material Selection
-
Step 2: Suitable Material Selection
We carefully select tungsten carbide rods with varying specifications and performance characteristics based on their intended uses. Our shank diameter tolerance is 0/-0.005mm, reducing vibrations during high-speed cutting.
-
Step 3:Produced by Walter
-
Step 3:Produced by Walter
We use Walter machines for both cutting tool production and re-grinding, and they perform excellently in terms of increasing efficiency. The Walter machine body has a high deadweight and rigidity, that effectively reduces vibration impact and ensures high grinding accuracy. With a stock of 24 grinding wheels, our machines can handle complex geometry structures and large-scale milling cutter production.
-
Step 4: Measure
-
Step 4: Measure
After the completion of carbide end mill production, we conduct a comprehensive test on each tool using Zoller equipment to measure every diameter, angle, and arc. All tools must pass the program's checks before they are sent to our QC department.
-
Step 5: Coating
-
Step 5: Coating
Coating is a chemical and thermal barrier that reduces diffusion and chemical reactions between the tool and the workpiece, thus reducing matrix wear. End mills that undergo coating have many advantages, including high surface hardness, good wear resistance, stable chemical properties, heat and oxidation resistance, low friction coefficient, and low thermal conductivity characteristics. Coated end mills have a cutting life increased by 3-5 times more than an uncoated tool, increased cutting speed by 20%-70%, improved processing accuracy by 0.5-1 level, and reduced total cost by 20%-50%.
-
Step 6: Package and Delivery
-
Step 6: Package and Delivery
Before packaging and shipping, our expert quality control team tests the tools for dimensions and surface finish to ensure they meet our high standards.
troubles shooting
Sometimes, we are encountering the problems when using the solid inserts, the following are the typical situations that you may face
cutting blade borken
Tool broken
-
1
Feed rate too high
reduce the feed rate
-
2
Cuttng direction is not right
changed the direction
-
3
Blade too sharp
chamfer and roundness the cutting edge
-
4
Tools not fixed well
checking and fixed the collet
-
5
Vibration
reduce the turning speed
-
1
too much cutting output
reduce the cutting parameter
-
2
Cutting resistance too much
reduce the feed ,increase the turning speed
-
3
Tools too long
Adjust the suitable tools
Wear too fast
-
1
Feed rate too low
increase the feed rate
-
2
Cutting direction is incorrect
changed the cutting direction
-
3
The hardness of material is too high
choose the suitable and right tools
surface roughness bad
-
1
Vibration
adjust the cutting parameter
-
2
Chip remove bad
adjust the enulsion ,increased the cutting speed
-
3
Feed rate too high ,but low turning speed
adjust the correct cutting parameter
Recycle and Regeneration of Carbide End Mills
Recycle with Re-grinding and Coating
We don’t just offer high-efficiency carbide end mills, we also provide recycling services through re-grinding and coating to reduce tooling costs. Normally, the grinding process only uses 20-30% of new tools but can increase the tool’s working life by over 70%. The proper coating also extends the tool’s life.
Regeneration and Coating
Are you concerned that old tools may no longer work with updated production processes due to changes in dimensions?
We offer regeneration services that update the diameter, shapes, and applications of tools to ensure compatibility with new production processes. The proper coating also extends the tool’s life.
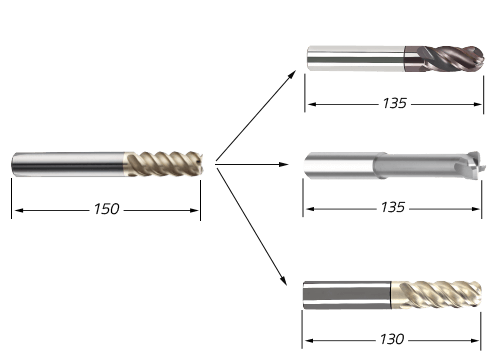