PCD End Mill
PCD end mills cutter for non-ferrous material
A rotary cutting tool with one or more cutting teeth used in milling operations is called a PCD end mill cutter. The PCD cutter’s tool body is typically constructed from high-speed steel or tungsten carbide. In milling machines, the end mill is typically used to process surfaces, steps, grooves, form surfaces, and cut workpieces after being tip-mounted with a PCD blade. The blade’s PCD material is a variety of polycrystalline diamonds.
High wear resistance, low friction, and high hardness are all characteristics of this substance. The diamond layer is mechanically supported by the tungsten carbide tool body, which also increases the diamond layer’s bending strength. In addition, the carbide layer can be used to make a variety of PCD milling cutter shapes because it can be easily tipped with a PCD blade.
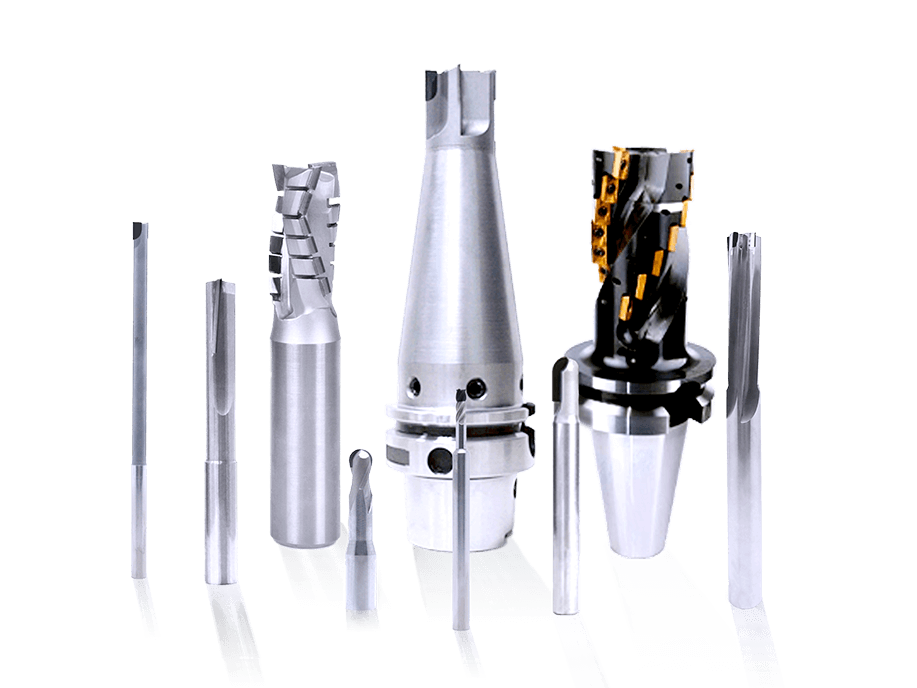
The Advantage of Using PCD End Mill Cutter
We design and manufacture PCD end mills for our clients worldwide. The wide range of our cutting tools serves several industries for precision machining of non-ferrous metals and non-metallic material to achieve the parts requirement finish and accuracy.
When processing copper, zinc, aluminum, and other non-ferrous metals, the processing material is easy to adhere to the cutting tool, therefore, it will result in the working process being hard to go on. Because of the lower friction coefficient and affinity with non-ferrous metals, Our PCD end mills can efficiently prevent the metal from bonding with the tool. Meanwhile, our PCD tool cutting edge deformation is small, and the surface of the workpiece is excellent like polishing.
- High Accuracy and Efficiency
- High-speed Cutting Feed Rate
- Excellent Roughness
- Fewer Process Steps Low cycle time
- Maximum tool life
- Re-grinding to reduce the cost
The most typical six types of PCD End Mill Cutter
Connect with the Sundi Tools Sales Team
Choose the Proper PCD end mill cutter for your application
For decades, our business has concentrated on high-end, precise production. We offer consumers top-tier tool items and technical support solutions through technological innovation and high-quality production services. Sundi’s influence is a result of both our ongoing efforts to promote advanced precision manufacturing applications and our capacity to provide cutting-edge value.
The following materials can be machined using PCD end mills from our experienced engineering team:
Al
aluminum and aluminum alloy
High hardness, lower coefficient of thermal expansion small affinity when milling
Cu
Copper and copper alloys
High working efficiency and the working surface can be smooth as a mirror.
CFPR
Carbon fiber reinforced plastic
Efficiently avoid delamination and fracture defects, and ensure the milling stabilities
Ceramic
Ceramic
Abrasion resistance 10 times of ceramic workpieces, small thermal wear resistance during machining.
Gr
Graphite Composites
High size accuracy is guaranteed and the working life can reach 30,000-40,000 pieces.
High-Level Qualified Raw Material
Our tungsten carbide bodies are sourced from high-quality companies, and our PCD blades come from E6, ensuring stable cutting performance.
Un-equal flutes Design against the Vibration
Flutes with sharp cutting edges and an uneven design can boost PCD end mill sets' cutting effectiveness by up to 300%.
OEM Service
We welcome you to mark your own logo or packaging.

Advanced Processing Technology
Our factory uses Walter, 5-axis Vollmer, and Zoller machines to ensure consistent dimensions and to prevent tool collision with a chamfered radius.
Optimize Process to Improve Efficiency
The engineering team will design different R Angle specifications according to the requirements of different occasions, to meet the accuracy and ensure lasting tool durability.
Custom-Made Service
We offer customization services based on specific processing workpieces and working conditions.
UseCase of PCD End mill
PCD Endmill with 6 flutes
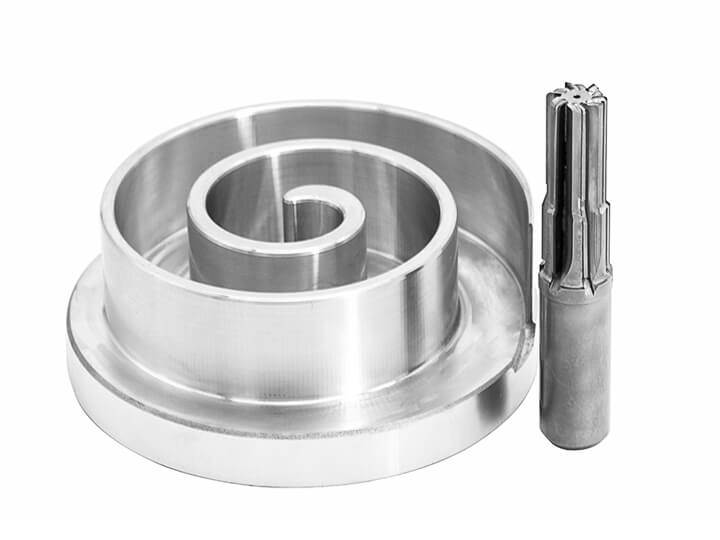
-
Profile Tolerance
+/-0.02mm
-
Perpendicularity
+/-0.01mm
-
Straightness
+/-0.005mm
-
Roughness
Ra0.6μm
-
Parallelism
+/-0.02mm
-
Flatness
+/-0.01mm
- Apply to machine air condition compressor scroll in the auto industry
- Faster cutting speed and Longer tooling working life
- Better surface finish and dimension accuracy
PCD End Milling for Carbon Fiber Sheet
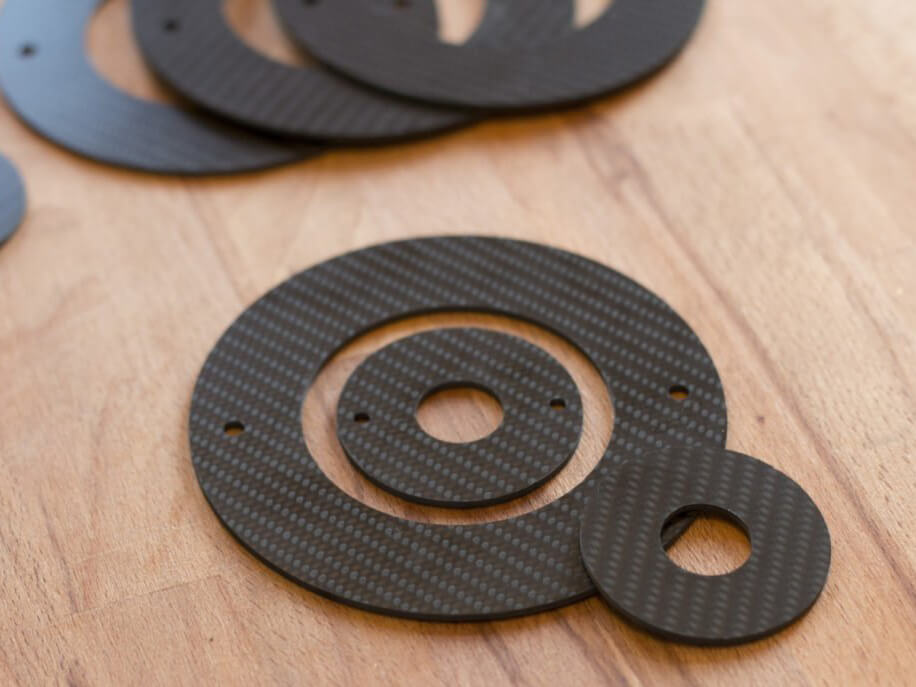
-
Workpiece
Carbon Fiber Sheet
-
Material
Carbon Fiber Reinforced Plastic (CFRP)
-
Machining Application
2 axis Milling
-
Diameter Range
Ø3-Ø20
- Avoid the breakage or layered
- Reliable and efficient performance
- Extends tool life, reducing tool sharpening and downtime
- Machining stability when processing CFPR
PCD Milling Cutter for Graphite composites
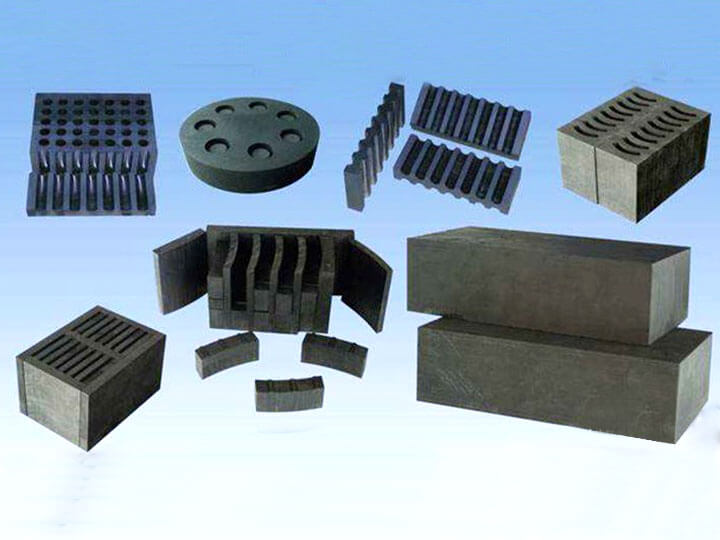
-
Workpiece
Graphite Electrode
-
Material
Graphite
-
Product Application
Molding
-
Selection
PCD blade
-
Parallelism
+/-0.02mm
-
Profile Tolerance
+/-0.02mm
- Avoid the cutting tool edge preparation
- A suitable geometric angle design Helps reduce tool vibration
- PCD blade with Wear resistance performance greatly extends the tooling life
Connect Us Now
How Do We Produce the PCD End Mill Cutter
-
Step 1 Aalysis and Design
-
Step 1 Aalysis and Design
With consumer plenarily communication, Deepens know consumer requirement, According to consumer requirements, including accuracy, roughness, working life. We will fabricate qualified PCD milling tools for different applications.
-
Step 2 Rough Machining
-
Step 2 Rough Machining
It mainly includes tool body performing and chip grooves’ making. The manufacturing machining contains CNC turning and milling, cylindrical grinding,5-Axis CNC making the flutes, and heat treatment.
-
Step 3 Laser Cutting
-
Step 3 Laser Cutting
The laser machine cuts the PCD disk into small, linked blades using software calculations and arrangement. Laser cutting guarantees that each blade is the same size, which is useful for the next stage.
-
Step4 Vacuum Brazing
-
Step4 Vacuum Brazing
Before brazing, we will attach the PCD blades to the brazing grooves using silver solder. They are then placed in a vacuum brazing furnace and baked for 20 minutes at a temperature of 800 degrees. This process ensures that the silver solder is completely melted and securely attached. As a result, the PCD tips will not fall off even during high-speed turning or under strong impact.
-
Step5 Wire Cutting
-
Step5 Wire Cutting
Using the 5-axis Due to its great performance, ease of use, and stability, Vollmer Wire Cutting is one of the best ways for generating PCD-forming cutting tools, allowing us to finish all types of difficult PCD milling tool projects. The cold-oil processing environment considerably improves the cutting finish of the blade, and the surface finish can attain Ra0.4. We have three sets of Vollmers on hand to help with any project.
-
Step 6 Cylindrical Grinding
-
Step 6 Cylindrical Grinding
Sometimes, there is a requirement for smoothness when processing the aluminum holes. Therefore, we need to grind the cutting edge. On the one hand, this process can improve the PCD finish significantly, but on the other hand, a less sharp cutting edge reduces the vibration of the hole wall, Most important of all, tight accuracy to be within 0.002mm after cylindrical grinding.
-
Step 7 Measure
-
Step 7 Measure
After completing the wire cutting or grinding process, we will perform a comprehensive test on the tool using Zoller, checking every diameter, angle, and arc. The program must verify all measurements before the tool is passed to our quality control team. For some cutting tools with HSK and BT shanks, a dynamic balance test is required to ensure the PCD milling tool's concentricity is within 0.002mm while rotating.
-
Step 8 Surface Treatment
-
Step 8 Surface Treatment
This is the final step in the process. Based on the specific requirements of our customers, we offer surface sandblasting or oxidation treatment for PCD milling tools. The main purpose of this process is to ensure a visually appealing surface and prevent rust. Additionally, laser marking is available for different model information as per customer demands.
frequently asked questions for PCD end mill cutter and catalogs
FAQ
Most frequent questions and answers
Please click the contact form, submit your contact information, then describe your detailed requirements and upload the files with PDF, Dxf, or step. Our professional engineers will contact you within 12 hours
Please do not worry, click the contact form, and please describe your needs in detail, our technical engineer will contact you after receiving it. Free
We are very sorry that all reamers are custom-made according to the customer’s requirements. So we don’t have any in stock.
The delivery time depends on the complexity of the tool, the size of the tool size, and the purchasing quantity. we usually take about 15-20 days to finish them.
Dear customers, We will 100% inspect all dimensions of every PCD end mill before shipment, and generate detailed inspection reports. We will deliver to you together with the tools.
We placed great emphasis on the safety, timeliness, and efficiency of transportation. So we only cooperate with the best international logistics companies, such as DHL, UPS, and FedEx. We can accept EXW, FOB, DAP, DDP, and other service terms.
We are a direct tooling manufacturer, and T/T transfer is available. For the sample with a small amount, we can also accept credit cards, papal, western union, etc.