How to Choose the Right Tool Coating
Selecting the perfect tool coating might seem like a nuanced art, but it’s crucial for maximizing the efficiency and lifespan of your tools. Whether you’re a seasoned machinist or new to the field, understanding the variables that impact your choice will help you make an informed decision.
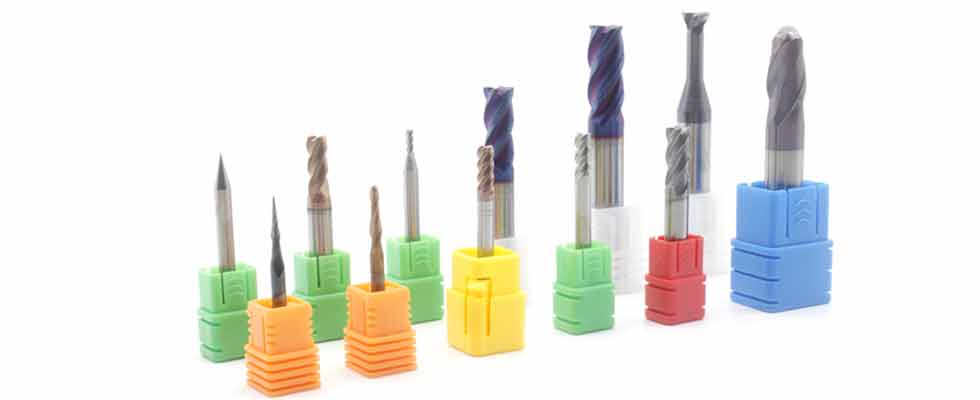
Understanding Tool Material
First things first, consider the material of the tools themselves.
- Carbide Tools
Carbide tools are popular due to their hardness and durability. Common coatings for these tools include Titanium Nitride (TiN) and Diamond-like Carbon (DLC), which enhance their performance by providing additional hardness and reducing wear.
- High-Speed Steel (HSS) Tools
HSS tools, while not as hard as carbide, are more versatile. Coatings like Titanium Aluminum Nitride (TiAlN) are excellent for increasing their wear resistance and operating life, especially under high temperatures.
Understanding Traditional Coatings
Traditional transition metal nitride coatings, such as TiN and CrN, have long been widely used due to their ability to improve tool hardness, toughness, and lifespan. However, the increasing demands of modern manufacturing conditions and the need for higher cutting precision have pushed the development of more diversified and functional coatings. New types of tool coatings, boasting higher hardness and better high-temperature oxidation resistance, have emerged as significant advancements in the field.
- Titanium Nitride (TiN) Coating:
TiN is one of the most common coatings produced using Physical Vapor Deposition (PVD) technology. It enhances tool hardness, toughness, and lifespan while offering a relatively high oxidation resistance temperature. TiN coatings are corrosion-resistant, oxidative, and wear-resistant, making them suitable for high-speed steel cutting tools or forming tools, ensuring quality machining.
- Titanium Carbide (TiC) Coating:
TiC was one of the earliest developed single coatings, boasting higher hardness than TiN. It offers strong mechanical wear resistance and strong adhesion to the substrate, which helps reduce machining resistance and cutting temperatures. However, its drawbacks include brittleness, low toughness, and bending strength, making it suitable for tools experiencing intense wear and continuous cutting.
- Titanium Carbonitride (TiCN) Coating:
TiCN is a ternary coating that incorporates carbon into the TiN lattice, replacing some nitrogen atoms. This addition enhances the frictional and wear properties, with carbon acting as a lubricant to reduce frictional wear. However, TiCN coatings may degrade at temperatures above 400°C, thus they are best used for high-speed steel tools operating below this temperature.
- Titanium Aluminum Nitride (TiAlN/AlTiN) Coating:
In this composite coating, aluminum replaces some of the titanium in the basic TiN structure, forming a cubic NaCl structure. The presence of alumina within the coating reduces thermal conductivity, thereby improving the high-temperature operational life of tools. TiAlN offers higher hardness, oxidation temperature, and thermal stability than TiN coatings, making it suitable for high-speed dry cutting of cast iron, stainless steel, and high-temperature alloys.
- Aluminum Titanium Nitride (AlTiN) Coating:
AlTiN differs from TiAlN in the ratio of aluminum to titanium. This coating is extensively used in wear-resistant applications due to its excellent mechanical and thermal properties, attributed to higher aluminum content. AlTiN coatings provide reduced wear and longer impact cycles, making them ideal for high-speed machining.
- Chromium Nitride (CrN) Coating:
CrN coatings are popular for their high hardness, thermal stability, and resistance to wear and corrosion. The large grain size and high deformation of the CrN structure can provide micro reservoirs for lubricants, making CrN suitable for components that operate under lubricated conditions. Its excellent anti-adhesion properties make it a preferred coating for tools used in cutting titanium alloys, aluminum, and other soft materials.
- Diamond Coating:
CVD diamond coatings are well-established for tools used in machining non-ferrous materials, providing optimal performance for cutting ceramics, graphite, metal matrix composites (MMC), high silicon aluminum alloys, carbon-carbon composites, and highly abrasive materials. However, pure diamond coatings lose hardness and carbonize at high temperatures and have a strong affinity for iron, making them unsuitable for machining steel parts to avoid damaging the adhesive layer between the coating and the tool.
- Cubic Boron Nitride (c-BN):
Cubic boron nitride, synthesized under high pressure and temperature, is second only to diamond in hardness and thermal conductivity. It is especially effective for machining ferrous materials due to its excellent chemical and thermal stability. c-BN coatings are ideal for machining hard cast iron, hardened steel, high-temperature alloys, and hard metals, often making them the best choice for challenging materials.
Each type of tool coating has its specific applications, further enhancing the tool’s lifespan through various structures such as single-layer, double-layer, multi-layer, compound, gradient, nano-coatings, and nano-composite coatings, tailored to different machining processes like cutting, drilling, gear rolling, and threading
-Advantages of Tool Coating
The primary advantage of tool coating is the significant extension of tool life. Coated tools perform better and last longer, even under tough conditions, by providing a barrier that minimizes wear and tear and enhances overall tool efficiency.
-Types of Tool Coatings
Common types of coatings include Titanium Nitride (TiN), which offers great hardness and resistance to wear; Diamond-Like Carbon (DLC), known for its low friction and high hardness; and Ceramic coatings, which are favored for their heat resistance and hardness. Understanding these options helps users choose the best coating for their specific needs.
Application of Tool Coatings in Various Industries
In aerospace, tools must withstand extreme conditions; therefore, advanced coatings such as TiAlN are used to handle high temperatures and reduce wear during critical manufacturing processes.
Aerospace Industry Coatings
In aerospace, tools must withstand extreme conditions; therefore, advanced coatings such as TiAlN are used to handle high temperatures and reduce wear during critical manufacturing processes.
Automotive Industry Coatings
In the automotive sector, coatings like DLC are preferred for their ability to reduce friction and wear, which is crucial for manufacturing engine components and other critical parts.
Cost vs. Performance
While more advanced coatings like Diamond and c-BN offer superior performance, they come at a higher cost. Evaluate the necessity based on the tool’s usage frequency and the machining conditions.
Conclusion
Choosing the right tool coating is about balancing the type of tool, the material being machined, the machining environment, and the specific application. By considering these factors, you can greatly enhance the performance and lifespan of your tools.
FAQS
Q:What is the best coating for high-speed steel tools?
A:TiAlN is highly recommended for high-speed steel due to its thermal resistance and durability.
Q:Can any tool coating be used for any material?
A:No, coatings are specific to the type of material being machined. For instance, Diamond coatings are ideal for non-ferrous and abrasive materials.
Q:How do I choose a coating for dry machining?
A:Look for coatings like TiAlN that can handle the heat generated from friction, such as in dry machining.
Q:What is the most cost-effective tool coating?
A:Titanium Nitride (TiN) is generally the most cost-effective and provides a good balance of performance and durability for general applications.
Q:Are there environmentally friendly tool coatings?
A:Yes, coatings like DLC are considered environmentally friendly due to their lower environmental impact during production and use.