Powerful Insights into Hydraulic Tool holders
Hydraulic tool holders are becoming increasingly popular in various industries due to their precision, accuracy, and durability. These tool holders play a critical role in manufacturing and other industrial applications, offering benefits that surpass traditional tool-holding methods. This article explores the many aspects of hydraulic tool holders, focusing on their use, benefits, and future trends.
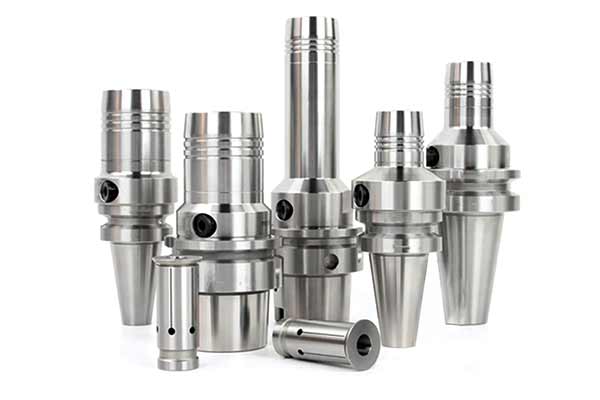
Notes on the Use of Hydraulic Tool holders
Hydraulic Chucks offer significant advantages in multiple industries due to their unique design and capabilities. They are designed to provide a strong and consistent grip, which is crucial in high-precision environments. Let’s delve into the specific uses and applications of hydraulic tool holders in industrial settings.
Hydraulic chucks are commonly used in CNC (Computer Numerical Control) machining, where precision is vital. Their hydraulic-based clamping system ensures a firm grip on tools, reducing vibrations and enhancing accuracy during high-speed operations. This makes them ideal for applications where even the slightest error can have significant consequences.
Beyond CNC machining, Hydraulic Chucks are also employed in other areas such as metalworking and woodworking. In these environments, the secure clamping mechanism minimizes the risk of tool slippage, improving safety and reducing downtime due to tool-related issues.
Hydraulic Chucks are also valued for their ability to accommodate a wide range of tool sizes and shapes. This versatility allows manufacturers to use a single toolholder for multiple tools, reducing costs and streamlining operations. Additionally, the hydraulic clamping system provides consistent pressure, ensuring a reliable grip across different tool types.
- Benefits of Hydraulic Tool holders
The benefits of Hydraulic Chucks are numerous, making them a popular choice among manufacturers and engineers. Here’s an overview of some of the key advantages:
- Precision and Accuracy: The hydraulic clamping mechanism ensures a secure grip on tools, reducing vibrations and enhancing precision. This results in higher-quality products and fewer defects during manufacturing.
- Reduced Tool Wear: Hydraulic tool holders offer a uniform clamping force, minimizing tool wear and tear. This leads to longer tool life and reduced replacement costs.
- Quick Tool Changes: Hydraulic tool holders are designed for easy tool changes, allowing operators to switch tools quickly without compromising precision or safety.
- Vibration Reduction: The secure clamping system reduces vibrations during high-speed operations, leading to smoother cutting and machining processes.
- Versatility: Hydraulic tool holders can accommodate various tool sizes and shapes, providing flexibility in manufacturing processes.
With these benefits, it’s clear why hydraulic tool holders are gaining popularity across industries. Their combination of precision, durability, and versatility makes them an ideal choice for many applications.
- Comparing Hydraulic Tool holders to Other Types
Hydraulic Chucks offer unique advantages compared to other types of tool holders, such as collet chucks and shrink-fit tool holders. Let’s examine some of the key differences:
- Clamping Force: Hydraulic tool holders provide a more consistent and uniform clamping force than collet chucks, which rely on mechanical pressure. This consistency results in better precision and accuracy during operations.
- Ease of Use: Unlike shrink-fit tool holders, which require heating and cooling for tool changes, hydraulic tool holders allow for quick and easy tool swaps. This convenience can lead to significant time savings in a production environment.
- Reduced Tool Wear: The uniform clamping force in hydraulic tool holders helps reduce tool wear compared to collet chucks, which can apply uneven pressure. This results in longer tool life and reduced maintenance costs.
While each type of tool holder has its benefits, hydraulic tool holders offer a balance of precision, ease of use, and durability that makes them a preferred choice in many industrial applications.
Precision and Accuracy in Hydraulic Tool holders
Precision and accuracy are critical in manufacturing and other industrial settings. Hydraulic Chucks excel in these areas thanks to their unique design and functionality.
The hydraulic clamping mechanism in these tool holders ensures a firm grip on tools, minimizing vibrations during high-speed operations. This stable clamping force translates into greater precision and accuracy during machining processes. Whether cutting metal or shaping wood, hydraulic tool holders offer the stability needed for precise results.
Additionally, the consistent clamping force reduces the risk of tool slippage, further enhancing accuracy. This is particularly important in CNC machining, where even the smallest deviation can lead to defects or rework. With Hydraulic Chucks, manufacturers can achieve higher-quality products with fewer errors.
Applications of Hydraulic Tool holders in Industry
Hydraulic Chucks are used in a variety of industries due to their precision and versatility. Let’s explore some of the common applications where these tool holders excel:
- CNC Machining: Hydraulic tool holders are widely used in CNC machining due to their ability to provide a secure grip and reduce vibrations. This leads to more accurate and precise cuts, resulting in higher-quality products.
- Metalworking: In metalworking, Hydraulic Chucks offer a strong clamping force, reducing tool slippage and enhancing safety. This is crucial in high-speed metal-cutting operations.
- Woodworking: Hydraulic tool holders are also used in woodworking, where precision and accuracy are essential. Their versatility allows for quick tool changes, making them ideal for complex woodworking tasks.
These are just a few examples of where hydraulic tool holders are used. Their ability to provide consistent clamping force and accommodate various tool sizes makes them a popular choice across industries.
- Manufacturing with Hydraulic Tool holders
Hydraulic tool holders are a valuable asset in manufacturing, offering a range of benefits that contribute to efficient and accurate production processes. Here’s how they play a role in modern manufacturing:
- In manufacturing, precision is key. Hydraulic Chucks ensure a firm grip on tools, reducing vibrations and enhancing accuracy. This leads to more consistent cuts and fewer defects, ultimately improving product quality. Additionally, the quick tool change capabilities of hydraulic tool holders allow for greater flexibility in manufacturing, enabling operators to switch between tasks with ease.
- Another advantage is the reduced tool wear. Because hydraulic tool holders apply a uniform clamping force, tools experience less stress and wear over time. This not only extends the life of the tools but also reduces replacement costs, contributing to overall cost efficiency in manufacturing.
- Hydraulic Chucks also enhance safety in manufacturing. The consistent clamping force reduces the risk of tool slippage, minimizing the chances of accidents during high-speed operations. This safety aspect is crucial in manufacturing environments where worker safety is a top priority.
- Maintenance and Longevity of Hydraulic Tool holders
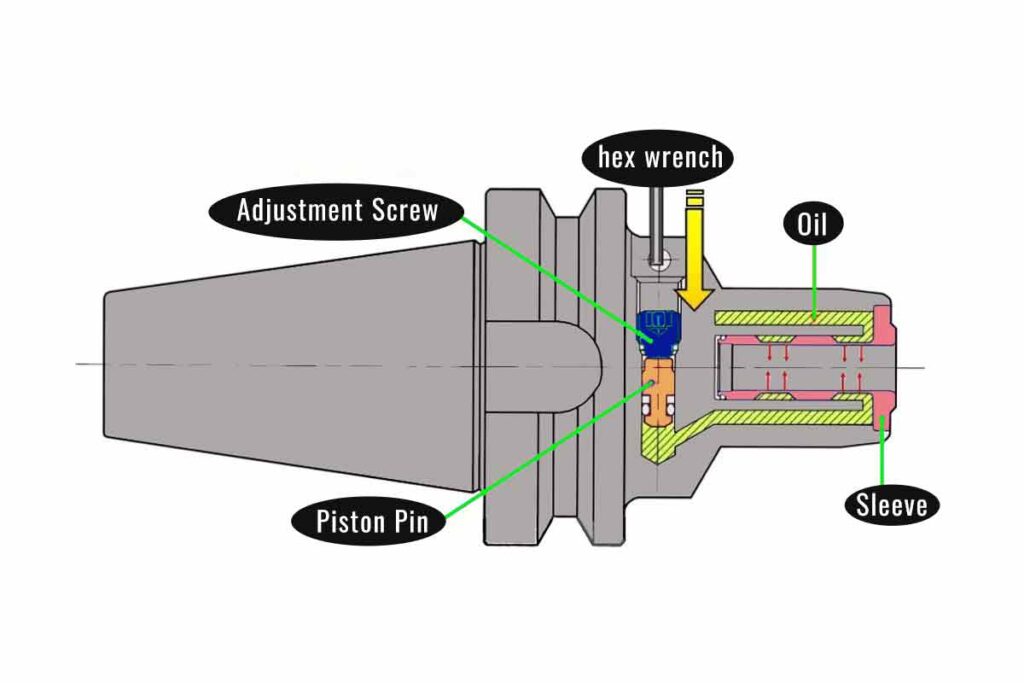
- Hydraulic tool holders create significant pressure between the inner wall and the tool when tightened. Even minute debris can damage the inner wall, leading to difficult tool extraction, loss of precision, or tool slippage. Oil contamination can reduce hydraulic tool holder grip strength by over 50%.
- Shank tolerance for diameters smaller than 6mm is h5, while those larger or equal to 6mm is h6. Tools with shanks smaller than the lower tolerance limit are prone to slippage, damaging the tool or ruining the workpiece. Tools with shanks larger than the upper tolerance limit can be difficult to remove, affecting the tool holder’s lifespan.
- When a coated tool is inserted into the tool holder, the compressive stress during tightening may cause the shank coating to flake off, which can damage the inner bore of the tool holder, reducing its lifespan.
- Tightening the pressure screw without a tool inserted (dry tightening) can cause excessive deformation of the inner bore and lead to hydraulic fluid leakage, causing irreversible damage.
- Tightening the hydraulic tool holder’s bore can press into a tool’s shank notches, causing difficulty in tool extraction. This can lead to plastic deformation, making the tool impossible to remove or causing loss of precision, rendering the tool unusable.
- If tools touch the bottom of the tool holder during installation without axial adjustment screws, slight deformation during tightening can affect tool accuracy, reducing tool life and causing poor machining results.
- The ideal operating temperature for tool holders is 20°C–50°C, with a maximum of 80°C and a minimum of 10°C. Excessive heat can cause internal pressure to exceed the design maximum, potentially cracking the tool holder. Too low temperatures may result in insufficient internal pressure, preventing effective tool tightening.
- When tightening the pressure screw, constant compression and friction occur between the screw threads. Without adequate lubrication or cleaning, this can cause thread stripping or screw damage, making it impossible to remove. This is particularly problematic when the clamping cycle is frequent, the operating temperature is high, or there’s abrasive dirt or chips. Copper powder-containing molybdenum disulfide lubricant is recommended for optimal pressure screw lubrication.
- If a hydraulic tool holder hasn’t been used for a long time, its internal hydraulic system may require re-lubrication, leading to reduced hydraulic oil. Additionally, pressure screws might experience minute leakage during tightening. Clamping force should be rechecked in three instances: first-time use, after more than 100 uses, and at least once every three months.
Following these maintenance practices can help ensure that Hydraulic Chucks continue to perform effectively and have a long lifespan.
Choosing the Right Hydraulic Tool holder
Selecting the right hydraulic tool holder for specific applications can significantly impact performance and efficiency. Here are some guidelines to help you choose the ideal holder:
- Consider the Tool Size and Shape: Ensure the Hydraulic Chucks is compatible with the size and shape of the tools you’ll be using. A versatile tool holder that can accommodate different sizes is ideal for flexible manufacturing processes.
- Check the Clamping Force: Choose a hydraulic tool holder with a clamping force suitable for your applications. This ensures a secure grip and reduces the risk of tool slippage.
- Evaluate the Environment: Consider the manufacturing environment, including temperature and humidity, when selecting a hydraulic tool holder. Some tool holders may perform better in specific conditions.
- Look for Quick Tool Change Features: If quick tool changes are necessary, opt for a hydraulic tool holder with easy swap capabilities. This feature can save time and boost productivity.
Choosing the right Hydraulic Chucks involves understanding your specific needs and matching them with the appropriate holder features.
- Safety Considerations for Hydraulic Tool holders
Safety is paramount when using hydraulic holders. Here are some important safety tips to keep in mind:
- Secure Clamping: Ensure the holder is properly clamped to avoid tool slippage during operation. This reduces the risk of accidents and enhances safety.
- Regular Inspection: Regularly inspect the tool holder for signs of wear or damage. Replace any worn components promptly to maintain safety.
- Follow Manufacturer Guidelines: Always follow the manufacturer’s guidelines for operation and maintenance. This ensures safe and efficient use of hydraulic tool holders.
- Use Protective Gear: When working with hydraulic tool holders, wear appropriate protective gear such as safety glasses and gloves. This minimizes the risk of injury in case of accidents.
By adhering to these safety considerations, you can ensure a safer work environment when using hydraulic tool holders.
Trends and Innovations in Hydraulic Tool holders
The world of hydraulic tool holders is constantly evolving, with new trends and innovations emerging regularly. Let’s explore some of the latest developments in this field:
- Advanced Clamping Technology: Manufacturers are developing advanced clamping systems that provide even greater precision and stability. This leads to improved accuracy and reduced tool wear.
- Smart Tool holders: The integration of smart technology into hydraulic tool holders is gaining traction. These smart tool holders can monitor clamping force and other parameters, providing real-time feedback for optimal performance.
- Improved Durability: New materials and manufacturing techniques are increasing the durability of hydraulic tool holders. This means longer tool holder life and reduced maintenance costs.
- Customizable Designs: Manufacturers are offering customizable hydraulic tool holders to meet specific industry needs. This allows for greater flexibility in manufacturing processes.
These trends and innovations demonstrate the ongoing evolution of hydraulic tool holders and their increasing importance in various industries.
-Future of Hydraulic Tool holders
Looking ahead, the future of hydraulic tool holders appears promising with several exciting developments on the horizon. Here’s what we can expect:
- Increased Automation: Automation is likely to play a larger role in hydraulic tool holders, with automated clamping systems and smart technology enhancing efficiency and precision.
- Greater Versatility: Future hydraulic tool holders may offer even greater versatility, allowing for quick changes between different tools and applications. This can lead to more flexible manufacturing processes.
- Enhanced Safety Features: Safety will continue to be a focus, with advanced safety features and monitoring systems becoming more common in hydraulic tool holders.
- Sustainability: As industries focus on sustainability, hydraulic tool holders are expected to incorporate more eco-friendly materials and manufacturing processes.
The future of Hydraulic Chucks is bright, with technology driving innovation and improving the overall performance of these critical tools in various industries.
Conclusion
Hydraulic tool holders play a crucial role in manufacturing and industrial processes, offering precision, accuracy, and versatility. From CNC machining to metalworking, their unique clamping system provides a secure grip, reducing vibrations and tool wear. As technology continues to evolve, hydraulic toolholders are poised for even greater innovation, with trends pointing toward increased automation, enhanced safety features, and sustainability. By understanding the benefits and proper use of Hydraulic Chucks, industries can continue to improve efficiency and product quality.
FAQS
Q:What are hydraulic toolholders used for?
A:Hydraulic toolholders are used in manufacturing and industrial settings to secure tools during machining processes. They offer precision, accuracy, and reduced tool wear, making them ideal for CNC machining, metalworking, and woodworking.
Q:How do hydraulic toolholders work?
A:Hydraulic toolholders use a hydraulic clamping mechanism to grip tools securely. This system provides consistent clamping force, reducing vibrations and enhancing precision during high-speed operations.
Q:What are the benefits of hydraulic tool holders?
A:Hydraulic toolholders offer several benefits, including precision, accuracy, reduced tool wear, quick tool changes, vibration reduction, and versatility. These advantages make them a popular choice in various industries.
Q:Are hydraulic toolholders better than other types of toolholders?
A:Hydraulic toolholders offer unique advantages over other types, such as collet chucks and shrink-fit toolholders. They provide a more consistent clamping force, are easier to use, and reduce tool wear. However, the choice depends on specific applications and preferences.
Q:How do I maintain hydraulic toolholders?
A:To maintain hydraulic toolholders, conduct regular inspections, clean and lubricate them, calibrate the clamping force, and replace worn parts promptly. Proper maintenance ensures the longevity and effective performance of hydraulic toolholders.
Q:What are the safety considerations for using hydraulic toolholders?
A:Safety considerations for hydraulic toolholders include ensuring secure clamping, conducting regular inspections, following manufacturer guidelines, and wearing appropriate protective gear. These precautions help maintain a safe working environment.